Condition Monitoring
As the name suggests condition monitoring relates to the monitoring of parameters in machinery or systems as a basis of identifying an existing or developing condition. Just as the human body has symptoms which help a doctor identify fitness, condition monitoring gazes machine or system fitness through measurable parameters. Condition Monitoring or as iAdept refers it to as Predictive Reliability introduces planning into your maintenance requirements and schedules.
While most believe condition monitoring is a cost group, we have increasingly proven the profit / return benefits of deploying technology to judge reliability. Predictive reliability technologies mitigate major looses owing to unexpected failures or downtimes. With scheduled downtimes parts inventory and production losses are a thing of the past. Parts can be ordered when needed avoiding escalated costs & wastage; production losses vanish and finally but most significantly, a failure leading to healthy parts damage, production losses, cost of un-utilized salary is totally avoided.
Components of Condition Monitoring are wide spread with diverse applications for inferring body, machine, material and structural health. Application and usage and expected output by use of specific technology depends heavily on the expert. Technology decision depends on circumstances, environment, materials and functional criticality. Hope you see the connect between Condition Monitoring and Predictive Reliability term coined by iAdept.
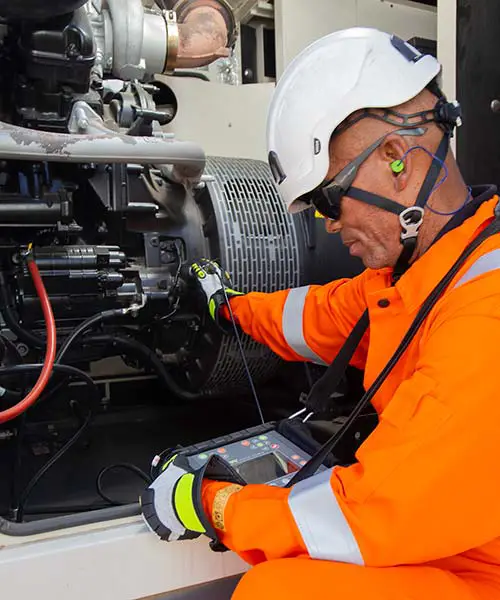
Condition Monitoring / Predictive Reliability Technologies:
Vibrations are movement usually identified as shaking around a focal point. As an example seen in the case of a moving part or parts within a machinery or system. Manufacturers goto great lengths to eliminate vibration as its neither desirable nor good for a machine or system. Vibrations can not only be measured but also understood for reasons and repercussions. Prominent examples of Vibrations exist in engines, motors, pumps, turbines etc leading to noise, efficiency losses, parts damage etc.
- iAdept has pioneered the Vibration Analysis and Diagnostics field for over one and a half decade. Not only did we begin with the division in the beginning but also were the first to develop a fully functional and globally competent Diagnostic Software VibAnalyst-TM (Linked to VibAnalyst page)
At iAdept, we understand that even minor imbalances in rotating machinery can lead to major issues like excessive vibration, noise, bearing wear, and premature failure. Our expert balancing services ensure that all rotating components—such as fans, pumps, blowers, motors, and turbines—operate within acceptable vibration limits.
We offer both static and dynamic balancing, using advanced tools and techniques to correct imbalance on-site or at our facility. By identifying the exact weight and location of imbalance, we apply precise corrections that restore equipment stability and performance. This not only extends the life of your machinery but also improves safety, reduces energy consumption, and lowers operating costs.
Balancing plays a crucial role in preventive maintenance and asset reliability. With iAdept’s balancing expertise, you can achieve smooth, uninterrupted operations, minimize unplanned downtime, and protect your investments in critical equipment.
Proper alignment is essential for the efficient and reliable operation of rotating machinery. At iAdept, we offer precision laser alignment services to ensure that coupled machines—such as motors and pumps or generators and gearboxes—are perfectly aligned. Misalignment can cause serious damage over time, including excessive vibration, bearing failure, shaft damage, and energy loss.
Our trained engineers use high-accuracy laser alignment tools to detect angular and offset misalignment in both horizontal and vertical planes. By correcting these issues, we help our clients achieve smoother operation, lower maintenance costs, and increased machine uptime.
iAdept’s alignment solutions are critical during equipment installation, post-maintenance checks, and troubleshooting. Whether you’re commissioning new systems or optimizing existing ones, our alignment services help you reduce wear, improve energy efficiency, and extend the lifespan of critical components. Trust iAdept to bring precision, reliability, and longevity to your rotating machinery.
Vibration monitoring is at the core of predictive maintenance—and iAdept excels in providing comprehensive solutions to detect and diagnose machine health issues early. Our services cover both periodic monitoring and continuous real-time monitoring using high-quality vibration sensors, portable analyzers, and integrated software platforms.
We track parameters like overall vibration, velocity, acceleration, and displacement to identify faults such as imbalance, misalignment, looseness, bearing wear, and gear mesh problems. Our team of vibration analysts interprets the data to provide actionable insights, trend reports, and recommendations that prevent equipment failure and unplanned downtime.
Whether you’re monitoring a single asset or implementing a plant-wide vibration strategy, iAdept provides tailored solutions that fit your needs. By integrating vibration monitoring into your maintenance program, you enhance reliability, improve safety, and increase operational efficiency. With iAdept, you’re not just monitoring machines—you’re protecting your productivity and maximizing asset performance.
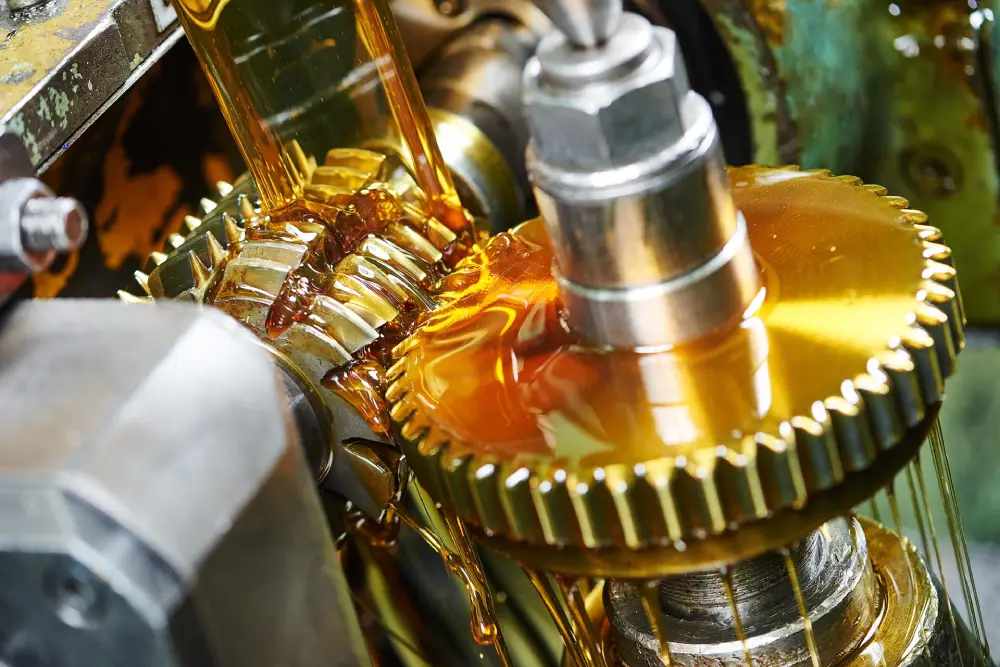
- Lubricant Analysis: Analysis of lubricants and oils is usually an offline process conducted through a lab analyzing lubricant properties, suspended contamination and wear debris. Part of Industrial Tribology study, Lubricant Analysis is usually done via continuous sample analysis monitoring trends over machine life span. A recognized and capable lab and a strict analysis plan for trend identification is all that is needed for Lubricant Analysis and related judgement.
- iAdept though does not promote lubricant analysis as a support mechanism, however has that as an offering for existing customers for ease of dealing with a single partner. iAdept works with leading players as an outsourced partner for Lubricant Analysis.
- Motor Current Signature Analysis (MCSA): The origins of the concept can be traced back to 1970’s when it was initially proposed for use in nuclear power plants for inaccessible motors or the ones placed in hazard zones. The technique befits from use within normal working and load conditions without operations interruptions. MCSA is a method from wider field of Electrical Signature Analysis (ESA) utilized for generator, power transformers & electric equipment beyond electrical induction motors that MCSA deals with.
- MCSA detects the following faults:
- Stator faults (opening or shorting of coils of stator windings) & abnormal windings
- Bent Shaft which could be catastrophic owing to friction between rotor and stator
- Bearing and gearbox faults
- Broken or cracked rotor bar or end rings
- Air gap irregularities static and/or dynamic
- iAdept offers products dealing with Motor Current Signal Analysis. We understand the need to constantly monitor the signals for early detection of faults. We understand the benefits of coupling MCSA as a technique in collaboration with Vibration and Thermography and encourage simultaneous as well.
- The technique utilizes information from current and voltage signals across all three phases simultaneously. While Motor Current Signal Analysis monitors single stator current thus deploying one of the three phases of motor supply current and using motor stator windings as transducers, MBVI utilizes all three phases and establishes a mathematical relation between voltage and current. Applying the model and using measured voltage, a modeled current is created to compare with actual. Deviations thus highlight imperfections in the motor or equipment which can be analyzed using Park’s vector, Fourier analysis & algorithmic assessment of resultant spectrum. These are permanent solutions rather than a short term diagnostic system.
- iAdept is all about solutions and MBVI systems are part of the offerings which help resolve problems related to motors and electrical equipment
Calibration as a field deals with accuracy measurement and alignment to approved standards of your test and measurement equipment. iAdept has been helping companies improve accuracy of their measurement devices for well over a decade. Calibration services have been carried out both on-sight and off sight as the case may be. The importance of equipment calibration isn’t only required for audit approvals but is also well established process to ensure efficiency isn’t compromised.